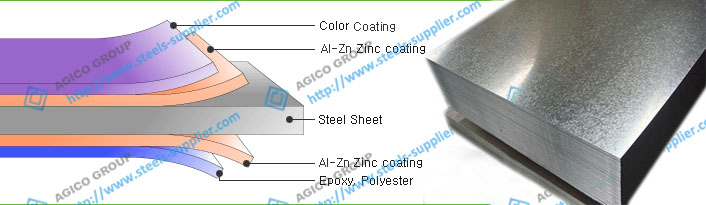
Why use Zinc to produce galvanized steel coil
Zinc is a blue-white metal having a melting point of 419.4 ° C and a density of 7.14 g/cm 3 . Zinc has moderate ductility. Zinc does not change in dry air at room temperature. In the moist air, the zinc surface forms a dense film of zinc carbonate, which protects the interior of the zinc from corrosion. Since zinc has such an excellent property, zinc is plated on the surface of the steel sheet to prevent corrosion, and this steel sheet is called a galvanized sheet.
Advantages of Galvanized Steel Coil
After the steel coil or plate is galvanized, the service life can be greatly extended. If the zinc layer on the steel sheet is not destroyed, the zinc can prevent the corrosive medium (water, oxygen, carbon dioxide, etc.) from contacting the surface of the steel sheet, which is exactly the same as the anti-corrosion effect of the tin plating layer. However, if the galvanized layer is destroyed and the iron of the individual parts is exposed to the surface, since the chemical properties of zinc are more active than iron, zinc and iron form micro-batteries during the etching process, and zinc is the anode of the micro-battery. It is dissolved, and iron is protected by the cathode.
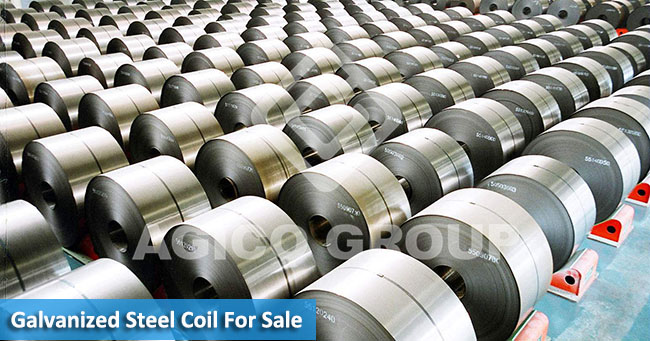
Therefore, the galvanized vessel will not rust even if it is partially exposed to iron. If the iron surface is exposed too much, the iron is corroded like ungalvanized. It can be seen that the galvanized sheet has good anti-rust properties and is widely used in the construction, vehicle, furniture, mechanical, electrical and packaging industries.
Steel Strip Galvanizing
Steel strip galvanizing is available in both electrogalvanized and hot-dip galvanized. The strip produced by the electroplating method has a thin coating but a complicated process.
What is the production process of hot-dip galvanized sheet?
The hot-dip galvanizing sheet production method is developed from the hot tin plating production method and can be roughly classified into the following types:
The term "out-of-line annealing" means that the raw material (hot and cold-rolled sheet) is first subjected to recrystallization annealing before entering the hot-dip galvanizing line; the so-called in-line annealing means that the steel sheet is first subjected to recrystallization annealing on the hot-dip galvanizing line. Then hot galvanized.
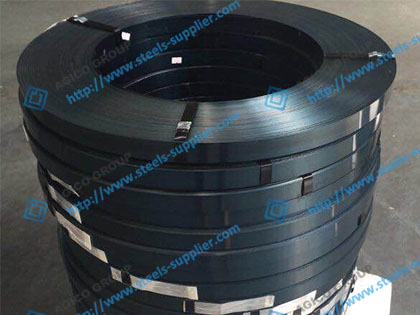
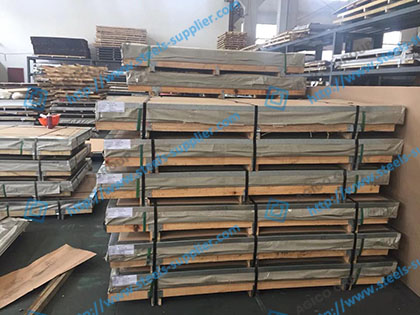
At present, the Sendzimir method, also known as the oxidation-reduction method is widely used. After cold rolling, the steel is directly sent to the hot-dip galvanizing unit. The steel strip is first burned in the continuous annealing process, and a thin oxide film is formed on the surface of the strip, and then passed through the reduction section of the annealing furnace. The oxide film on the surface is reduced to a pure iron body, so that the plating layer is well bonded to the iron base when entering the zinc pot.
For a 1700mm continuous hot dip galvanizing unit. The equipment layout and operation of the feed section and the discharge section of the unit are basically the same as those of the continuous electroplating tin unit. The continuous hot-dip galvanizing unit process section includes four main processes: pre-plating (degreasing and heat treatment), hot-dip galvanizing, and correction and passivation. The speed of the unit is 10-180m/min.
The 1700mm continuous hot-dip galvanizing unit adopts the method of degreasing annealing of the rapid heating furnace. The maximum temperature of the annealing furnace is up to 980 °C, and the annealed strip enters the zinc tank at a temperature of 450-470 °C to keep the temperature of the zinc liquid constant. Control the thickness of the coating by “air knife method”, that is, using a controllable nozzle at the outlet of the zinc tank to blow compressed air or superheated steam to the strip at a certain angle to remove excess zinc liquid, and in this way, positive and negative can be produced. A thick galvanized steel sheet with different thicknesses on both sides. In order to form a layer of zinc-iron alloy on the surface of the original plate to make it have good elongation, the plate after galvanizing should be reheated (ie, through a coating annealing furnace), and the heating temperature is about 550 ° C.
Tip: In order to improve the corrosion resistance of the galvanized steel sheet, the strip steel should be passivated in chromic acid or phosphoric acid solution after cooling.
