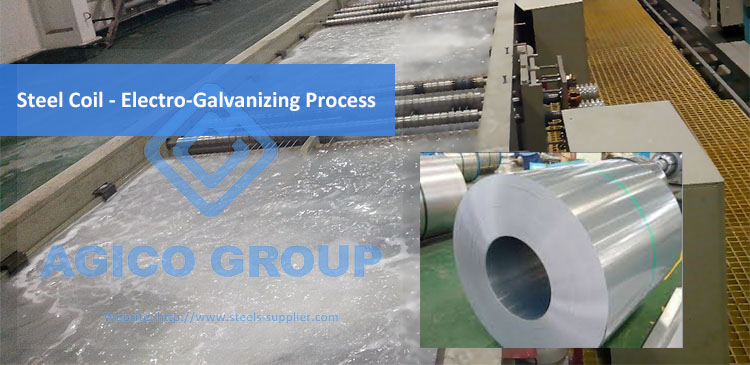
What is Cold Galvanizing and Hot Galvanizing
Cold galvanizing is also called electro-galvanizing. It is an electrolytic device that removes oil and pickles into a solution containing zinc salt and connects it to the negative electrode of the electrolysis device. A zinc plate is placed on the opposite side of the workpiece to be connected to the electrolysis device. The positive electrode, when the power is turned on, and the current is moved from the positive electrode to the negative electrode, a layer of zinc is deposited on the workpiece.
Hot-dip galvanizing is a method in which steel components are immersed in molten zinc to obtain a metal coating. The workpiece is degreased, pickled, dipped, dried and immersed in molten zinc. Time, just come up.
Principle Difference Between Cold Galvanizing and Hot Galvanizing
Basic Principles
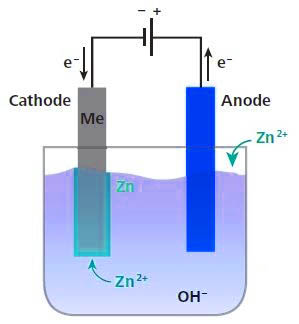
Cold galvanizing uses the chemical principle to separate the zinc alloy into zinc ions, which adhere to the surface of the steel. Generally, the zinc layer is thin, and the steel is easily rusted under normal environment. Generally, cold galvanizing is used for anticorrosion of various steel products and structures. The amount of galvanizing of cold galvanizing is very small, only 10-50 g per square meter.
It is well known that the mechanism of anti-atmospheric corrosion of zinc has mechanical protection and electrochemical protection. Under atmospheric corrosion conditions, there are ZnO, Zn(OH)2 and basic zinc carbonate protective films on the surface of the zinc layer, which slows down the corrosion of zinc to some extent. The protective film of the layer (also called "white rust") is destroyed and a new film layer is formed.
Principle Details:
When the zinc layer is seriously damaged and the iron matrix is endangered, zinc will electrochemically protect the matrix. The standard potential of zinc is -0.76V, and the standard potential of iron is -0.44V. When zinc and iron form micro-battery, zinc is dissolved as anode. Iron is protected as a cathode. The hot-dip galvanizing layer formation process is a process of forming an iron-zinc alloy between the iron matrix and the outermost pure zinc layer, and the surface of the workpiece forms an iron-zinc alloy layer during hot dip plating, which allows between the iron and the pure zinc layer. A good combination, the process can be simply described as: when the iron workpiece is immersed in molten zinc liquid (generally molten zinc liquid is about 455 ° C), first form a zinc and alpha iron solid solution at the interface. This is a crystal formed by the dissolution of zinc atoms in the solid state of the base metal iron. The fusion between the two metal atoms is relatively small.
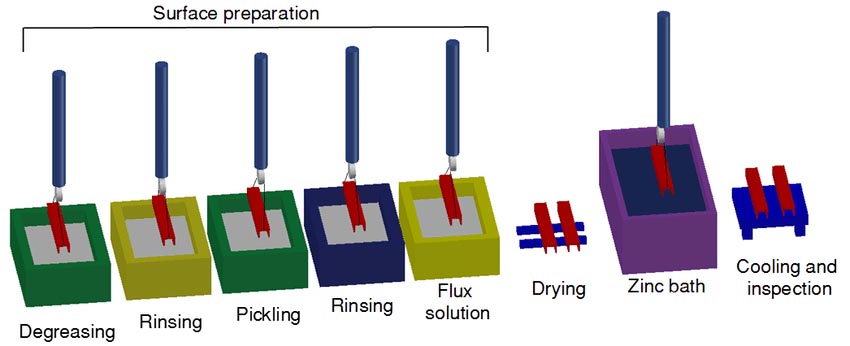
Therefore, when zinc is saturated in the solid solution, the two elements of zinc and iron diffuse into each other, and the zinc atoms diffused into (or called "infiltrated") the iron matrix migrate in the matrix lattice and gradually form with iron. The alloy, and the iron diffused into the molten zinc liquid forms a metal compound FeZn13 with zinc and sinks into the bottom of the hot-dip galvanizing pot, which is zinc dross. When the workpiece is removed from the zinc immersion liquid, a pure zinc layer is formed on the surface, which is a hexagonal crystal. The iron content is not more than 0.003%, the hot-dip galvanizing coverage is good, the plating layer is fine, and there is no organic matter inclusion.
